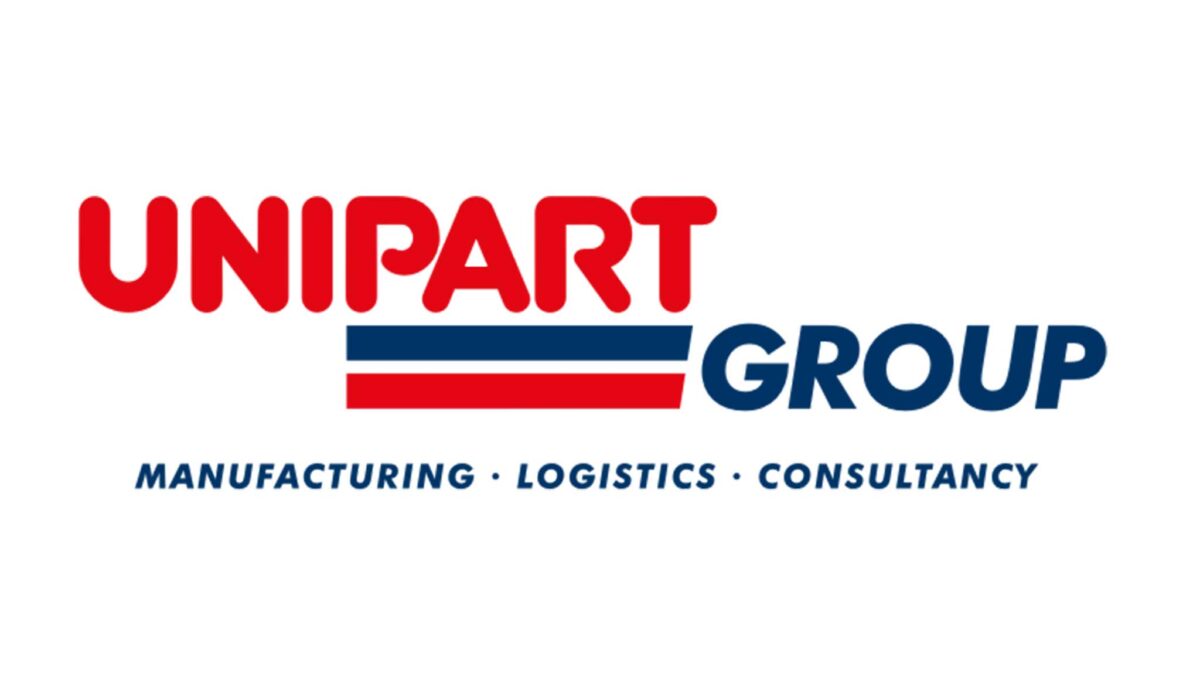
Hyperbat’s EV battery expertise wins £multi-million Lotus Evija contract
One of the UK’s leading manufacturers of high-performance electric vehicle battery packs has sealed a £multi-million-pound contract to supply batteries to Lotus for its new all-electric Evija, the world’s most powerful production car.
- Hyperbat, Unipart and Williams Advanced Engineering (WAE) joint venture, will supply battery packs to the all-electric Lotus Evija, the world’s most powerful production car
- The Hyperbat EV battery facility has been designed to support low volume, high-performance vehicles, and mid-volume specialist vehicle applications, in order to help its customers make the transition from internal combustion engines (ICE) to EVs
- Hyperbat has been developing and perfecting the battery technologies needed to contribute to Britain maintaining its place at the frontier of technological innovation in the automotive industry
Hyperbat was formed to bring together Williams Advanced Engineering’s (WAE) EV battery expertise with Unipart’s capability in manufacturing safety-critical products for premium OEMs. This combination of engineering excellence and Tier 1 manufacturing capability was established to support the scale-up of EV production in the UK and will manufacture the 90kWh lithium-ion battery packs destined for use in the first British-made all-electric hypercar.
Full production will take place at the firm’s brand-new production line at Unipart Manufacturing Group’s site in Coventry.
The mid-mounted battery pack will support a target output of 2000 PS and performance targets of 0-62mph in under three seconds and a top speed of over 200mph.
Andy Davis, Director at Hyperbat, said: “To win a contract with Lotus to supply battery packs for the world’s most powerful production car demonstrates the exceptional technology and manufacturing expertise we have at Hyperbat.
“This comes from decades of experience as a first-tier automotive industry manufacturer and is an example of how Hyperbat can continue Britain’s heritage at the frontier of technological innovation in the automotive industry, coupled with Unipart’s expertise in execution.
“Required performance levels will be facilitated by our proprietary welding and joining technologies, which, alongside the deployment of the latest digital technologies, are critical to achieving the highest levels of performance and product quality.”
The manufacturing process involves assembling 12,000 components split across 500 unique parts and 100,000 welds in each pack. This is a complex process for which Hyperbat employs a unique system using cameras, sensors and vision systems to monitor data for each of the battery components.
Andy continued: “We are one of the few companies to have invested in this advanced manufacturing technology which is enhanced by the research and development work carried out by the Institute of Advanced Manufacturing and Engineering (AME), who offer on-site support to our R&D team and are a perfect example of Industry and Academia working in partnership.
“This gives Hyperbat a digital advantage when it comes to highly complex battery manufacture for the world’s most demanding customers.”
Mark Edwards, Executive Director, Engineering, Lotus Cars, added his support: “We have been working with Unipart and Hyperbat for a number of years and are confident in their ability to deliver the quality of product and the level of Tier 1 manufacturing support Lotus needs for such a prestigious project.
“With this in mind, we are therefore delighted to appoint Hyperbat for battery production for Lotus’ first fully electric hypercar.”
Hyperbat has experience across a wide variety of high-performance road car and global electric motorsport programmes and is able to access this expertise and learning to support new customers.
The company is committed to selecting the best and most competitive supply solutions and is actively engaged with the Advanced Propulsion Centre to grow the UK’s EV supply chain capability through its “H1perChain” project.
Andy Davis added: “We are immensely proud to have been chosen as the battery manufacturer for this prestigious programme and are delighted to be delivering a premium battery for a premium application. Our success in battery manufacturing focuses on three things – getting the core processes right, ensuring repeatability and reliability of the complete manufacturing process, and accelerating speed to market.
“Hyperbat is now working with its shareholders and partners across government, industry and academia to ensure it continues to develop the skills needed for the UK to lead the way in battery manufacturing.”
James Hoxey, Commercial Director at Hyperbat, concluded: “We have spent the last few years developing and proving our capability, and this nomination is an important milestone for our business, enabling us to demonstrate what Hyperbat can provide to the market.
“The level of interest in the business and our capability is growing rapidly and further new business will undoubtedly follow.”
Hyperbat is part of a consortium of businesses using the latest 5G-enabled technology to speed-up its manufacturing processes. Partnered with BT, Ericsson and NVIDIA to benefit from the world’s first 5G virtual reality (VR) ‘digital twin’ solution, the company can leverage remote teams in different parts of the country to connect, collaborate and interact using a virtual 3D engineering model.
More in Manufacturing
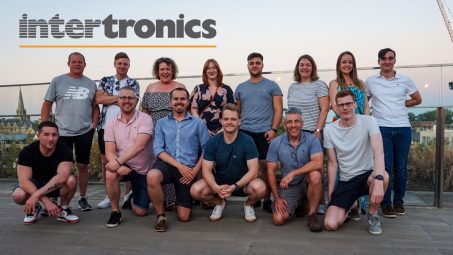
Intertronics: Driving Innovation in Adhesives and Assembly Solutions
For over four decades, Intertronics has been at the forefront of providing high-performance adhesives, coatings, sealants, and application equipment to industries that demand precision and reliability. From electronics and medical devices to automotive and aerospace, Intertronics’ expertise ensures that manufacturers can optimise their bonding and assembly processes with cutting-edge solutions.
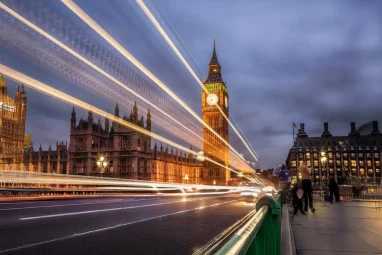
Unipart named CCS supplier
Unipart has been named as a supplier on Crown Commercial Service’s (CCS) Logistics, Warehousing and Supply Chain Solutions (RM6329) framework agreement.
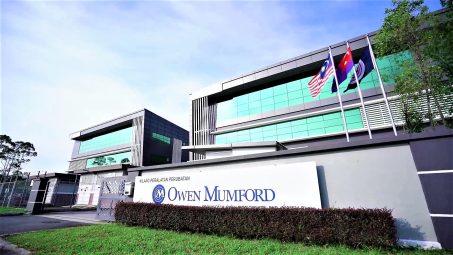
Owen Mumford: 70 Years of Innovation in Healthcare
Owen Mumford has been at the forefront of medical device innovation for over 70 years, pioneering solutions that enhance patient care and improve healthcare outcomes worldwide. Established in 1952 by Ivan Owen and John Mumford, the company has grown into a global leader in medical device design and manufacturing, with a commitment to quality, sustainability, and patient-centred innovation.
From this author
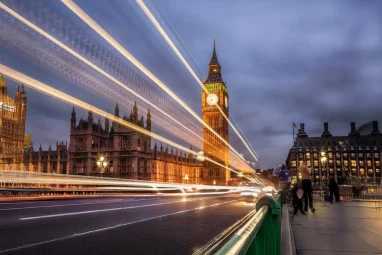
Unipart named CCS supplier
Unipart has been named as a supplier on Crown Commercial Service’s (CCS) Logistics, Warehousing and Supply Chain Solutions (RM6329) framework agreement.
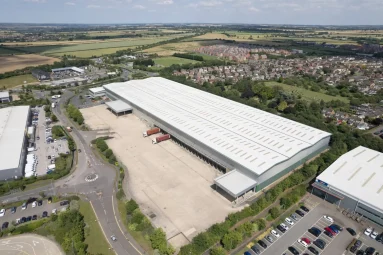
Unipart partners GBUK
Unipart has formed a strategic partnership with GBUK
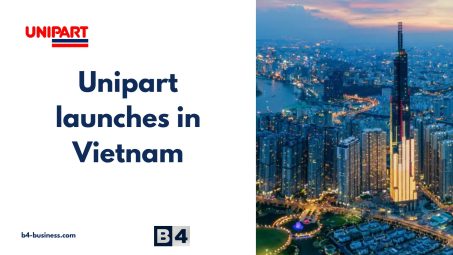
Unipart launches in Vietnam
Unipart, the supply chain performance improvement partner, has launched operations in Vietnam.