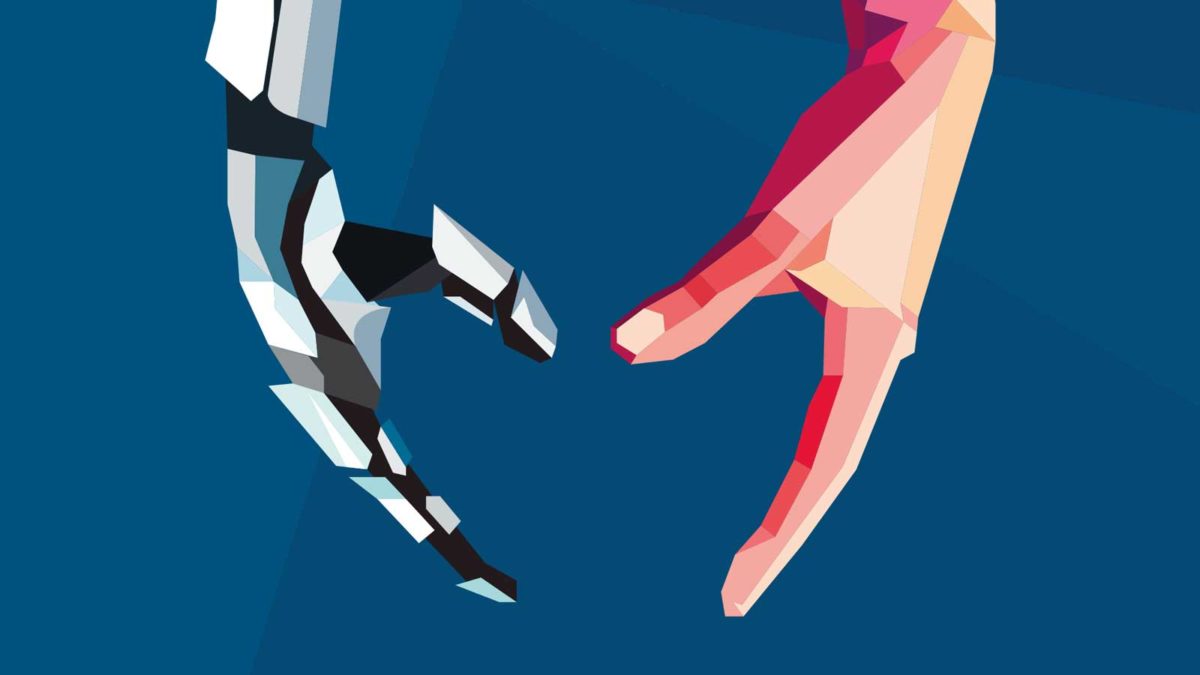
Future trends: Robotic Process Automation
The invisible robot army that will drive forward business productivity. One of the new tools of the future, in this age of Industry 4.0, will be Robotic Process Automation (RPA), and it has the potential to increase business efficiency and accuracy (as well as removing considerable cost).
Forbes forecasts spending on RPA to increase 60% this year and more recently the technology has been applied to unlock returns from expensive investments in Enterprise Resource Management (ERP) systems.
Well deployed ERPs drive forward business productivity and provide a consistent set of business information or ‘master data’ that allows complex business processes to run smoothly and in a synchronised way. They are sold on their potential to manage and integrate the business, improve information flows, aid decision-making, enable new services, improve process and operational efficiency, and minimise cost. Such is the reach and complexity of an ERP such as SAP ECC 6.0, that their selection, design, implementation and ongoing support can often involve very substantial investment.
Failing to generate returns
The hard truth is that many businesses fail to achieve all the planned returns from their investment in ERP. Often because of a lack of adoption by employees as a result of complex and difficult ERP user interfaces and poor training (often under resourced to minimise the cost of implementation).
With little support, and too big a hill to climb, employees fall back towards the familiar. Activities such as resource planning, forecasting and inventory management are once again managed in spreadsheets – many, many spreadsheets, often disconnected and invisible to other parts of the business. Crucially, all lack the advanced analytical tools and algorithms of modern ERP systems and break the link to a consistent set of master data.
Step forward RPA. Not the rise of an android workforce – but rather a software evolution involving programmed instructions that execute repetitive tasks quickly, accurately and at high speed. Whilst RPA has typically been used so far to automate tedious, repetitive back office processes, putting RPA between the ERP system and your workforce allows the user interface to be dramatically changed for the better.
The impact of RPA
Typically, RPA will enable complex, multiple user interface screens to be reduced down to just one or two, with only a fraction of the fields for the user to input information – the result is that the rate of work speeds up and, since RPA handles the error checking within the process, quality is improved too.
With staff able to now query and update the ERP within the warehouse or on the factory floor via mobile devices, the filling of forms for manual data entry later becomes redundant. Live production, inventory and customer order data is made available to those who need it, improving the organisation’s ability to make decisions and react to what is happening now.
Fast implementation
ERPs are known to be costly and time consuming to customise. RPA avoids this by simulating the interactions of an ERP user. This removes the need for expensive, additional licensing or heavy customisation of the ERP. A simplified, lightweight user interface can be built and delivered from within existing infrastructure or via the cloud, which interacts with the RPA system via an application programming interface (API).
RPA can also be rolled out iteratively. Key processes and workflows can be addressed first, with more implemented later. An iterative approach reduces the gap from initial concept to the delivery of business benefits.
Our prediction for the future is that more organisations will deploy RPA to get their users back onto the ERP and unlock the full value of their investment.
Getting started
The best starting point, like many digitalisation efforts, is to first map out your value streams. A common pitfall is to drop RPA into an existing, inefficient process in order to attempt to improve it. The risk is that this will limit the size of the potential prize. Starting with value-stream mapping provides the opportunity to re-engineer and remove waste and inefficiency from your processes, ready for RPA.
More in Manufacturing
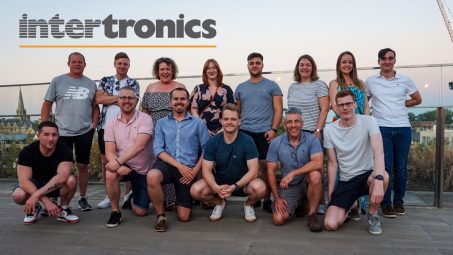
Intertronics: Driving Innovation in Adhesives and Assembly Solutions
For over four decades, Intertronics has been at the forefront of providing high-performance adhesives, coatings, sealants, and application equipment to industries that demand precision and reliability. From electronics and medical devices to automotive and aerospace, Intertronics’ expertise ensures that manufacturers can optimise their bonding and assembly processes with cutting-edge solutions.
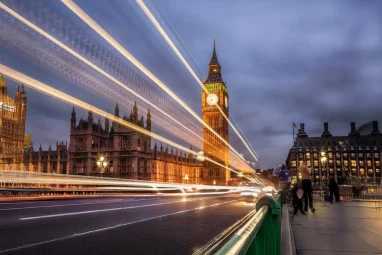
Unipart named CCS supplier
Unipart has been named as a supplier on Crown Commercial Service’s (CCS) Logistics, Warehousing and Supply Chain Solutions (RM6329) framework agreement.
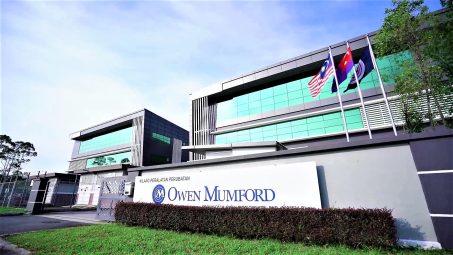
Owen Mumford: 70 Years of Innovation in Healthcare
Owen Mumford has been at the forefront of medical device innovation for over 70 years, pioneering solutions that enhance patient care and improve healthcare outcomes worldwide. Established in 1952 by Ivan Owen and John Mumford, the company has grown into a global leader in medical device design and manufacturing, with a commitment to quality, sustainability, and patient-centred innovation.
From this author
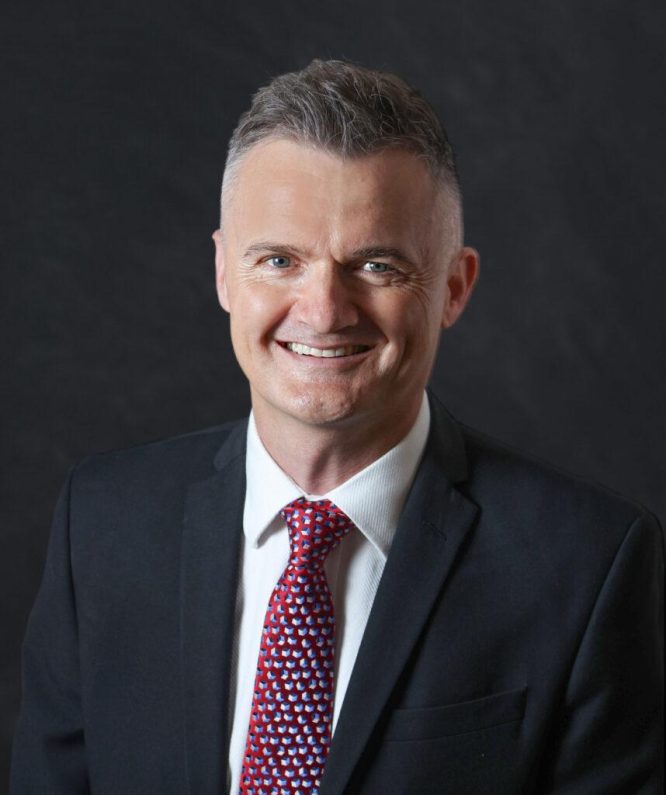
Unipart announces record performance for year ending 31 December 2024
Strong year of growth & expansion, celebrating 50 years of the Unipart brand
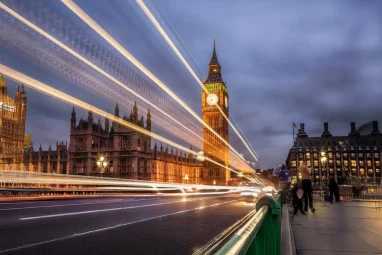
Unipart named CCS supplier
Unipart has been named as a supplier on Crown Commercial Service’s (CCS) Logistics, Warehousing and Supply Chain Solutions (RM6329) framework agreement.
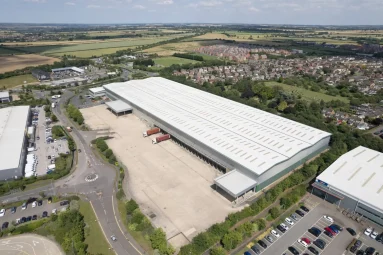
Unipart partners GBUK
Unipart has formed a strategic partnership with GBUK