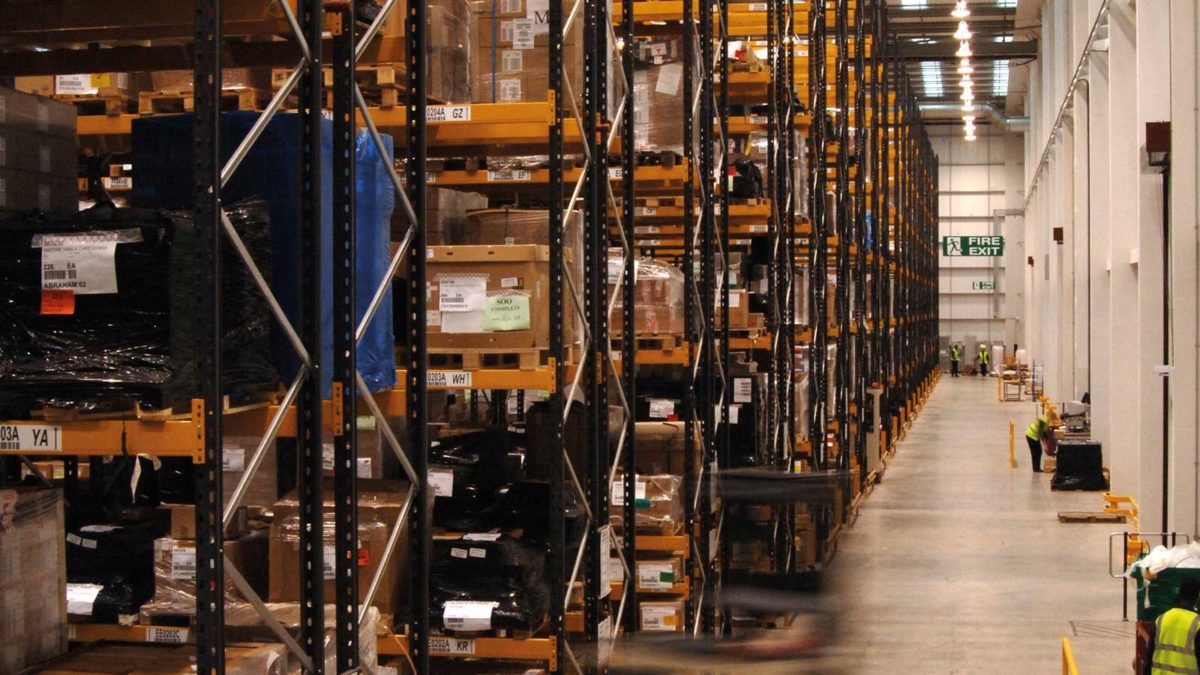
Helping you get a return on your investment from supply chain technology
While the right technology (applied in the right way) can make your supply chain incredibly efficient, many companies are struggling to ensure that they get a sound return on their investment.
Photography by: Unipart Group
Gone are the days when a single system or ‘killer app’ would deliver superiority in a sector. With the lightning fast pace of change in digital developments, a competitive advantage can be won and lost in a matter of weeks rather than years.
Unipart Group, one of Europe’s leading manufacturing, logistics and consultancy companies, has provided some useful questions that organisations should use in the evaluation process when choosing new technology:
1. How will it improve customer experience?
Only 3% of retailers say current systems ‘fully support efforts to improve the customer experience’. Enabling customers to see exactly where their shipments are provides reassurance and increases customer understanding of delivery schedules. Improving access to data for in-transit shipments is essential. End-to-end support for engineers, installers and delivery services provides a better overall experience for the customer while delivering efficiencies.
Utilising digital technologies has enabled Unipart to improve customer experience. For example, for one client they developed a smart van solution which improved tracking and controlling stock and equipment. The result was better equipped engineers who were able to deliver an improved customer experience.
2. How will it improve efficiency?
Supply chains are increasingly complicated and expensive. Increasing efficiency is an effective way to improve outcomes and drive down costs. Frictionless movement supported by complete and timely information can mitigate challenges from sudden shifts in demand, lack of raw materials or natural disasters.
Track and trace technologies such as electronic tagging through barcodes, RFID and sensors enable inventory to be tracked in real time – providing greater visibility, greater control and even preventing theft. Intelligent warehousing is enabling automation to be used effectively in the distribution centre, while augmented reality systems have delivered improvements in picking speed of up to 25%.
3. How will it help meet rising expectations of supply chain performance?
Customers are asking for increasingly complex services to be delivered by intelligent supply chains. For example, in the pharmaceutical industry, many companies are moving rapidly towards supplying patient services in addition to pharmaceuticals themselves. These services include delivery of medication – an area which has been identified as being highly valued by patients.
Given the requirements involved (for example, some medications need to be prepared just prior to delivery) this will necessitate a dramatic improvement in supply chain performance.
Unipart’s dynamic order fulfilment processes have been tailored to specific customer needs. For instance, when a major book retailer needed to increase numbers of individual titles while reducing stock levels, we helped to improve forecasting accuracy to 98%. This enabled an 8 a.m. next day delivery service (from central stock) for 65,000 titles.
4. How will it allow increased flexibility and scalability?
Increasingly, companies are expected to react quickly to changing customer and supplier needs, and even to personalise what they offer. Optimised supply chain management can be as important to success as actual product ranges or services. Technology holds the key to much of the optimisation work.
Honda is an example of a company which works around a demand-driven philosophy. It has set up its manufacturing systems to be flexible, so that it can match production to customer demand. If demand patterns shift, its factories are able to change the mix of vehicles produced in as little as 24 hours. That capability is partly down to a supply chain that is able to respond to such changes.
Similarly, just-in-time production logistics has enabled Unipart to work with other automotive manufacturers to ensure that they are fully equipped with the right quantity (and quality) of parts direct to line side, thereby minimising inventory and downtime.
5. How will it enable you to manage returns more effectively?
Omnichannel retailers – those which integrate the different methods of shopping available to consumers – are responding to consumer expectations, but face increased unpredictability as a result. Returns are costing retailers an average of £60bn a year, with over 30% coming from online sales.
Customers can order items online, by phone, or via retail and other physical locations. Those ordering remotely may order the same item in several different colours or sizes to try at home, and then return those items that they do not want to keep. To add to the challenge, online shoppers (in particular) expect fast service. Businesses therefore need supply, stock management and delivery systems that are able to deal with this level of complexity.
The average returned purchase passes through seven hands before it is listed for resale or recycle. Using an approach called Dynamic Dispositioning, Unipart has enabled its customers to reduce the time taken by the return cycle, while ensuring the maximum yield on returned items. By using advanced diagnostics and data analysis, Unipart also enables clients to minimise avoidable returns and repairs.
6. How will it help you comply with increasing regulation?
Trust is of growing importance to business, yet is harder for businesses to maintain. Customers are more socially, ethically and environmentally aware than they once were, and regulations are increasing. Businesses with complex global supply chains are under increasing pressure to meet these rising demands for transparency.
For instance, when a US-based guitar maker was deemed not to have sufficiently documented the sources of its imported wood, it was therefore unable to confirm that the company was not in violation of global sustainable forestry practices. The company was fined, stock was confiscated, and production disrupted.
Achieving real returns from technology investments requires more than just a box ticking exercise. However, the questions outlined above provide a starting framework that can guide you towards sustainable performance improvement of your supply chain. If you would like Unipart to help you on your company’s journey to a more efficient supply chain, get in touch with us by visiting our website www.unipart.com.
More in Manufacturing
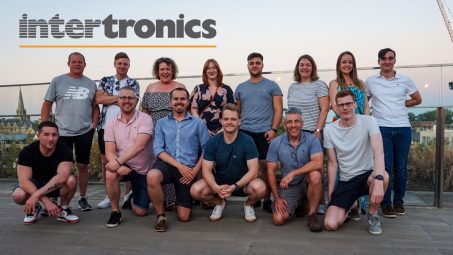
Intertronics: Driving Innovation in Adhesives and Assembly Solutions
For over four decades, Intertronics has been at the forefront of providing high-performance adhesives, coatings, sealants, and application equipment to industries that demand precision and reliability. From electronics and medical devices to automotive and aerospace, Intertronics’ expertise ensures that manufacturers can optimise their bonding and assembly processes with cutting-edge solutions.
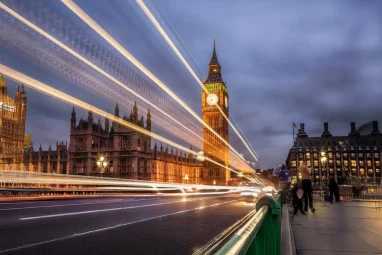
Unipart named CCS supplier
Unipart has been named as a supplier on Crown Commercial Service’s (CCS) Logistics, Warehousing and Supply Chain Solutions (RM6329) framework agreement.
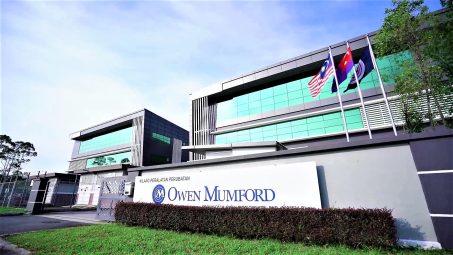
Owen Mumford: 70 Years of Innovation in Healthcare
Owen Mumford has been at the forefront of medical device innovation for over 70 years, pioneering solutions that enhance patient care and improve healthcare outcomes worldwide. Established in 1952 by Ivan Owen and John Mumford, the company has grown into a global leader in medical device design and manufacturing, with a commitment to quality, sustainability, and patient-centred innovation.
From this author
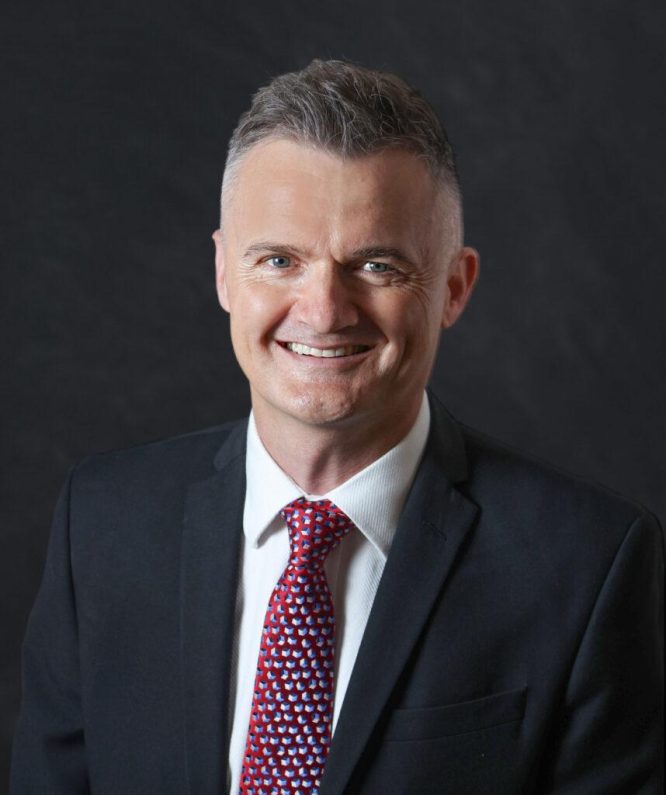
Unipart announces record performance for year ending 31 December 2024
Strong year of growth & expansion, celebrating 50 years of the Unipart brand
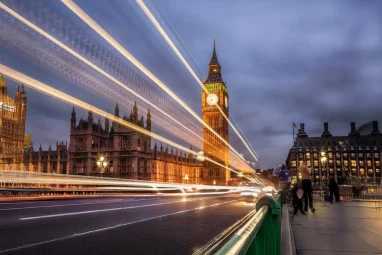
Unipart named CCS supplier
Unipart has been named as a supplier on Crown Commercial Service’s (CCS) Logistics, Warehousing and Supply Chain Solutions (RM6329) framework agreement.
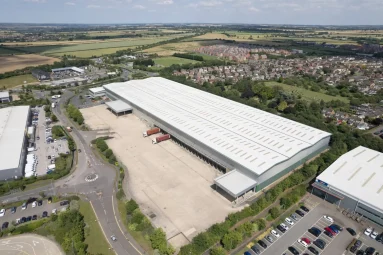
Unipart partners GBUK
Unipart has formed a strategic partnership with GBUK